LEAN - Continuous Process Improvement
Everyday a little up!“Do it right, do it better, do it differently”
LEAN is a deeply rooted philosophy of reflection and continuous improvement. Lean = Learn
“Lean thinking is a total business mindset focused on the elimination of anything in a process which does not add value to the output.
Value is defined by the customer.”
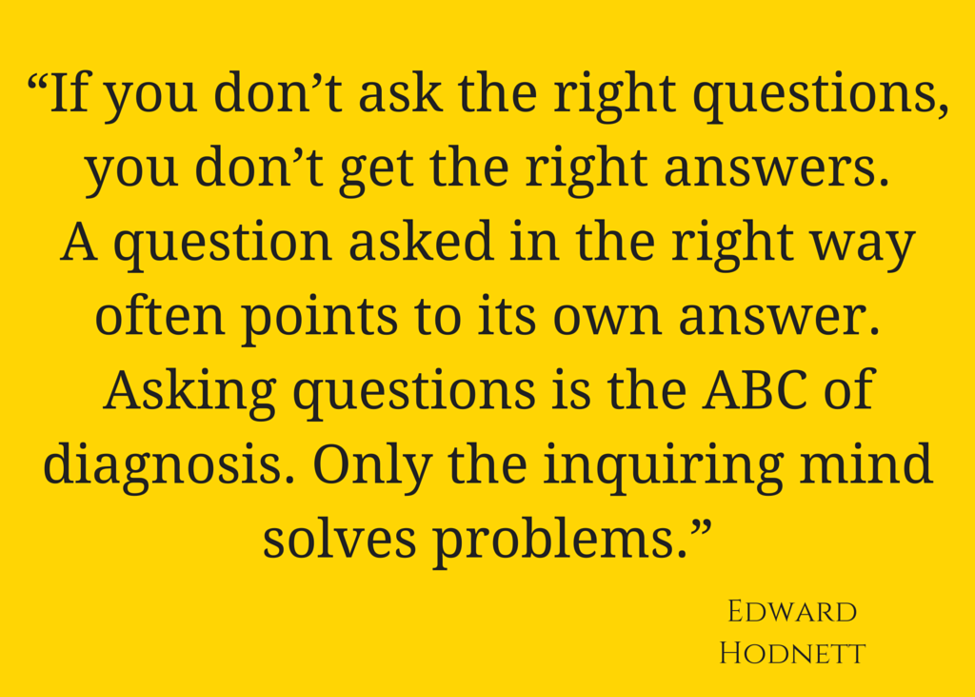
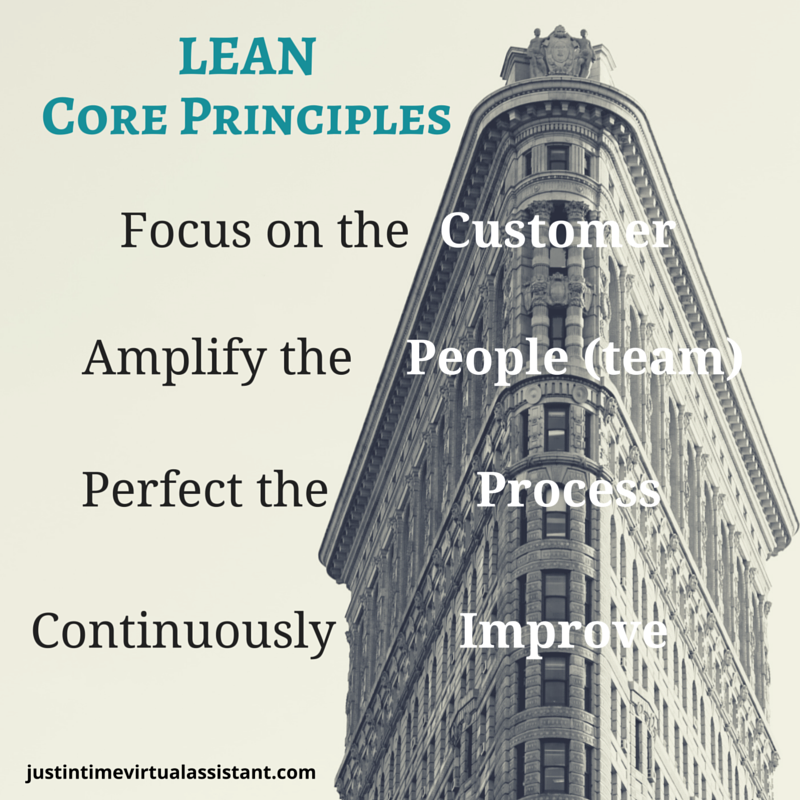
Key Concepts
- Standardization – eg – grouping, colour coding, standard locations, physical workplace set up, naming convention
- Quality at the source – preventing errors, build a culture where “stop” is as important as “go”
- Visual management – eg simple visual indicators Immediate awareness of standard and deviation from standard, correct it before the problem arises
- The 5 s’s – sort, straighten, shine, standardize, sustain – examples – eg household tasks
- Flow – the continuous addition of value. When you create flow, problems surface Pull – do something when it’s needed
- Just in time
- Pull vs push
- Gemba – go and see
- Elimination of waste
- Heijunka – leveling out the work
- Hurry up and wait – go slow to go fast (get it right first!)
- Quality/speed/cost = Golden triangle – All 3 need to balance
Administrative Support of Process Improvement Initiatives
If you’re running an efficient business then you have processes in place – maybe a lot of them!
Keeping these up to date and reflective of your current business ideals can be a challenge.
Just In Time can help with:
Formatting
Just a simple improvement like creating a clear repetitive format across all your processes can make a huge difference.
You may choose to add fields like these
- Who performs the task?
- Who is ultimately responsible?
- Frequency?
- Quality control?
Version control
Things are constantly changing and your business processes need to change to reflect this.
Keep your updates on file and visible using simple version control.
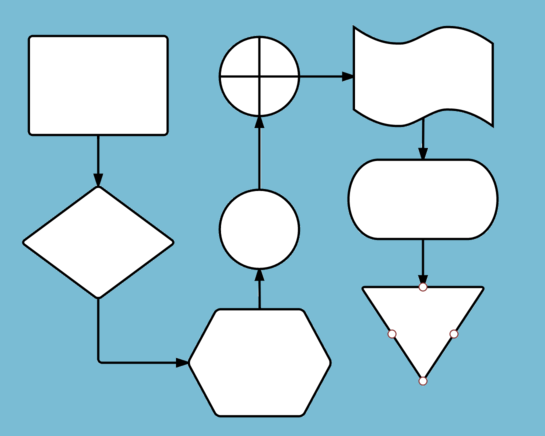
Flow Charts
Convert your text-heavy documents into efficient, step by step, visual flow charts.
Colour coding can be used to reflect systems or system statuses.
You may also choose to add swim-lanes to clearly define who does what and at which point in the process.
We use Lucidchart to draw our process flows.